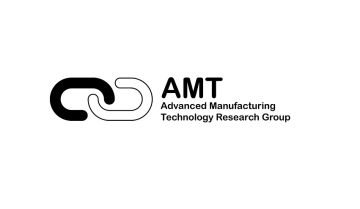
The Advanced Manufacturing Technology (AMT) Research Group was established in 1995 at the South East Technological University under the leadership of Mr Joe Phelan. Research in the AMT area is carried out at Masters and PhD level and is underpinned by a very active undergraduate project support structure.
Funding is through support and sponsorship from local and national industry and through the national competitive research grant system.
The AMT Research Group is the longest established research grouping in SETU Waterford and has a long list of successes in terms of graduates, funding and sustainable technical development.
The AMT research focus is in three main areas: Automated Systems; Precision Engineering and Microfluidics.
Automated Systems research focuses on flexibility and low-cost production through automation.
Precision Engineering research focuses on the development, control and applicability of precision system within industry.
Microfluidics research focuses on the design and applicability of low-cost chipset manufacturing processes.
Work continues as usual at undergraduate level, while AMT group members have recently supervised projects at postgraduate level in the automated systems and microfluidics areas as part of the MEngSc in Innovative Technology Engineering.
The group has recently re-focused on its links with industry and is currently progressing research postgraduate projects in the areas of process monitoring and control, and technological innovation in microfluidics.
Contact
Enquiries: Mr Liam O'Shea
Phone +353 51 302730
Fax + 353 51 302666
Email [email protected]
AMT Fulltime Faculty Members
-
Dr Jim Lawlor BTech, MSc, PhD
-
Mr. Liam O'Shea BEng, MSc
AMT Postgraduate Research
In the 2014/2015 academic year, there were 2 registered postgraduate students in the Advanced Manufacturing Technology Research Group – 1 studying at PhD level; and 1 studying at Masters level.
<h3><strong>Performing Innovation: Engineering a marketplace through the performative aspects of newly-envisioned technologies: </strong><em>J. Edwards (Jim Lawlor)</em></h3>
<p>Technological innovation can be perceived as a simple process, wherein an idea (science) needs only to have an appropriate technology applied (engineering), in order to achieve (market) success. In reality, the process is more complex, and requires a more sophisticated approach to optimize an innovation’s chances of success. The purpose of this interdisciplinary project is to examine this process in the context of the emerging microfluidics or ‘Lab-on-a-chip’ (LoaC) technological innovation. While concepts such as ‘creative destruction’ are well known in technological innovation, more recent work suggests that new technology markets emerge from a complex series of activities within a constantly changing environment. Within this volatile environment, the product and market inform each other’s development, transforming, and ultimately constituting the environment of which they become a part. Given this, and also the knowledge-intensive, capital-intensive and skills-intensive environment within which they tend to operate, this phenomenon is of particular interest to start-ups and spin-offs, and within new product development and research programmes.</p>
<h3><strong>Development of a generic tool condition monitoring validation methodology:</strong><em> B. Ronan (L. O’Shea)</em></h3>
<p> In precision engineering, cutting tool condition has a major impact on the accuracy and surface finish of machined parts. Currently, errors associated with tool wear are detected at the end of the machining cycle at which time the finished product is only of scrap value. This project proposes to bring validation techniques to bear on the tool wear aspect of machining, known as tool condition monitoring (TCM) with a view to improving the overall performance of the machining operation. This work is being performed in conjunction with an EU FP7 funded project that will install vision, acoustic and vibration sensors on selected machines in a tool-room environment.</p>
<p>The project aim is to produce a validation model for real-time TCM, which will be implemented on a fully functional factory floor demonstrator / prototype. The model will include the automatic selection and integration of numerous signals originating from several sensors, which comprise the TCM system.</p>
Lawlor, J, Kavanagh, D. (2015), ‘Infighting and Fitting In: Following Innovation in the Stent Actor-Network.’ Industrial Marketing Management, In Press.
A Case Study in Knowledge Creation, Jack Nunn and Liam O'Shea, IMC 30, NUI Dublin (Sept. 2013)
Lawlor, J. (2011), Competitive Activities in New Technology Industries. SETU Waterford Research Day, April 13, WIT.
Wallace, A., Phelan, J., Wemyss, T., Lawlor, J. (2010), A low-cost in-house laboratory-on-a-chip fabrication method. Lab-on-a-Chip European Congress, May 25-26, Dublin.